Tin-brass sandwich
As opposed to the pictures below, I had to solder all the layers together. I used an aluminium mandril wisible below for this. Each layer was first tin coated using soldering iron. Then all the layers were stacked on the mandril and heated on a stove and squeezed in a vise.
The method is very time-consuming and gives poor results. Given the choice, I would buy die-cast metal wheels next time.
How to get brittle wheels...
Each wheel consists of 5 layers of 0.5mm thick brass sheet metal.
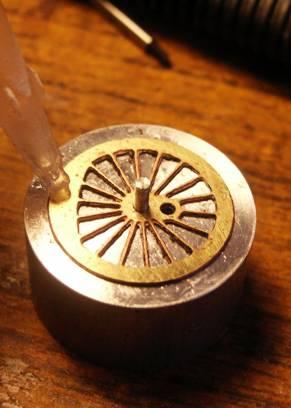
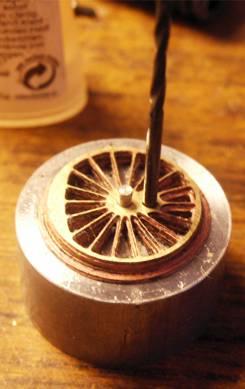
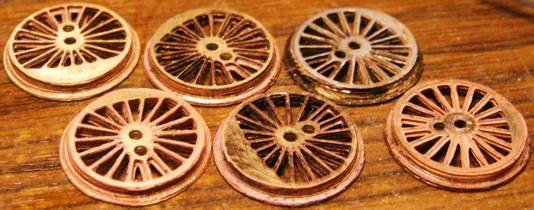
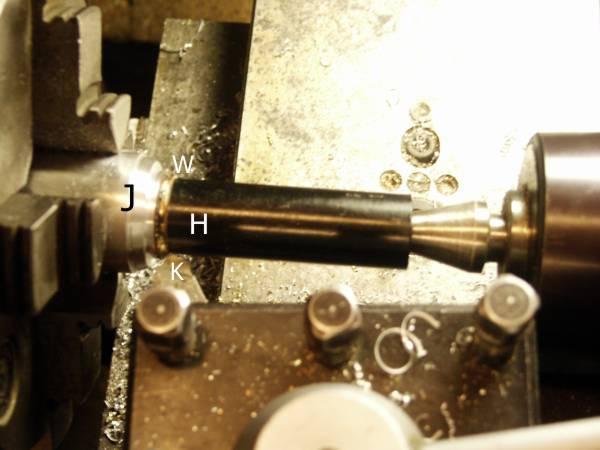
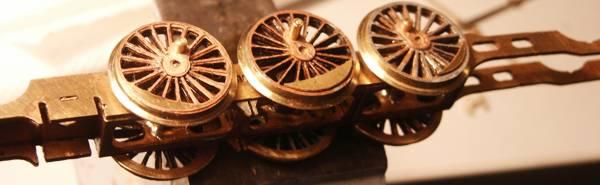